Valnes entered into a long-term cooperation with Krakul to develop a next-generation smart lock, also known as a digital access management system, capable of being controlled over the internet.
“We were looking for an engineering team to develop the hardware for Valnes’ smart lock system, which could be controlled remotely and provide a more comfortable platform for managing permissions. We announced a procurement and Krakul was the only company to offer a full-scale solution – from start to finish. Krakul’s references were impressive; they appeared in the spotlight through some of our mutual connections and ITL (Estonian Association of Information Technology).
Krakul was memorable with its “you name it, we’ll do it” approach. We liked how their team took the extra effort to understand where we are coming from and what Valnes is trying to achieve. Together, we mapped the specifications and requirements, and the development process started fairly quickly. Considering that the size of the system and the amount of data, user stories, was not small.
The development was a constant process with many iterations and variants. The first version still had lots of room for improvement, so throughout the years, we have together released over 20 different variants of the product while building upon our existing platform.
We would recommend Krakul as a partner for similar IoT projects. Our cooperation enabled us to realise the potential of a new business area where we are active to this day.
Working with Krakul always seemed more like a partnership than a client-developer relationship. Their team is highly competent, and it’s great to have a partner who manages more technical questions. Secondly, Krakul is very approachable. We didn’t have to put in a lot of effort to form a trusting relationship with their team; they excellently adapted to our needs from the start.”
Their Story
Taking lock security one step further
Valnes is a company engaged in the production and sales of locking and security products. They have over 27 years of experience in the design and installation of security locks, electric locks, door automation, and online access systems for various structures.
As of 2020, building material stores sell their products across Estonia, Latvia, Lithuania, Poland, and Finland. The turnover for 2019 was approximately 5 million euros.
Their Goal
An advanced system to manage door access via the Internet
Valnes has the ambition to become the market leader for smart locks. For that, they needed to develop a next-generation device that could manage the access of doors remotely. In essence, it would have to lock and unlock doors, administer the access rights with the date and time restrictions, delete keys when needed, change opening rights, and monitor the use of rooms and services – all via the Internet, using any computer or smart device.
By the time they approached us, they had already developed a version that worked similarly but had some issues regarding size, price, and connectivity. Thus they needed the help of an IoT developer who would be agile in helping them figure out a better end solution. At the same time, they were also hoping to find a long-term partner who would continue supporting the product after completion – which is precisely how we love to work with our clients.
Our Solution
Build a next-generation smart door lock for Valnes
Valnes’ team came to us with a clear vision and detailed specifications. In a nutshell, the main idea was to upgrade the previous version with all the necessary extra features, which would enable network connectivity.
The initial analysis was a long process. We designed specifications for the first version, but for the next six months, we had a meeting every Friday morning to discuss our possibilities. Valnes’ team had lots of great ideas, and our team supported them with the know-how. Throughout the analysis process, we offered a lot of suggestions for technical solutions and how we could build many versions of feature sets to save money from materials and labor.
As a result, the development plan was a combination of Valnes’ needs and our know-how. Together we reached an agreement on how the end solution should look like and which features should we integrate.
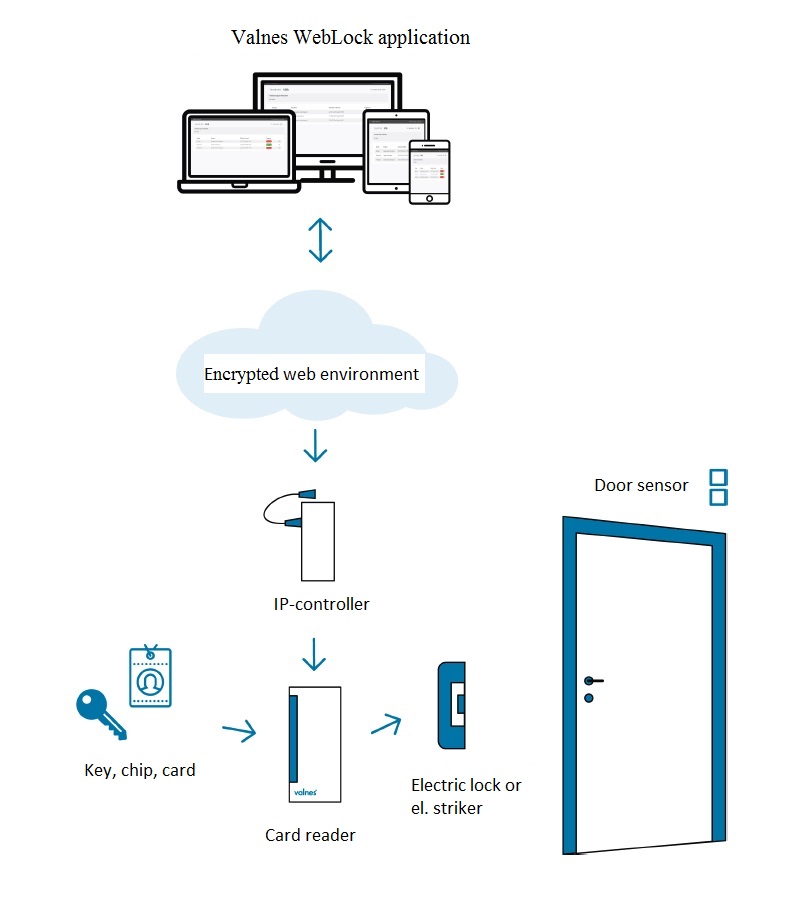
The initial plan for software development was to look at the previous version and break down what is already usable and what needs to be improved. The goal was to build a system capable of easily integrating with the previous version with the same level of functionality.
At the same time, our hardware team found that the best course of action is to keep the base functionality of the previous model and make specific improvements. Meanwhile, they had to be mindful of everything having to fit inside a preexisting case. In doing so, we had to add WIFI and NB-IoT (Narrowband – Internet of Things) capabilities, as well as other components necessary for guaranteeing network connectivity. All this proved to be quite a challenge since we had to fit remarkably more details inside the previous case.
The product development process for the hardware team looked like the following:
Creating an initial high-level schematic and system diagram in cooperation with Valnes’ team and concluding the client’s needs
- Creating the electronics schematics with the firmware team to avoid integration issues and correctly implement necessary features
- Produce PCB design, design the layout, carry out the routing, and assess mechanical constraints
- Ordering ready-to-go prototypes
The software development was structured accordingly:
- Creating a software architecture board, breaking down the most significant sections of the development process, and mapping the communication between different components and data acquisition
- Writing necessary code and implementing server communication that would communicate the same way as the previous version
- Programming necessary firmware functions into prototyping boards and testing how they work
- Live demonstration and client testing
The biggest challenge throughout the development process was the requirement for the product to be integrative between 11 different versions of the product. Since the device had to be multifunctional between a wide range of Valnes’ products, we put extra care into compatibility.
The size constraint proved to be the biggest challenge. As mentioned, the end product had to fit into the previous version’s case with a lot more components. Therefore, we had to do a lot of rethinking and redesigning to ensure functionality and maintain a great user experience.
We did rigorous testing across all iterations and physically implemented them in various locations to collect data about long-term use. During testing, we found out that there was a recurring problem with NB-IoT capability since narrowband coverage in Estonia had not developed enough by that time. The cycle of testing NB-IoT in total took about nine months.
After producing a viable product, we started working with EMSs to acquire data necessary for optimisation. Our team managed the whole manufacturing process and optimised the need for materials.
The first order was about 110 devices, of which 82% worked as intended, mainly due to manufacturer errors. We solved the problem by switching our EMS partner.
Today, we continue supplying Valnes with our smart lock devices. We designed a manageable production test jig, where testing for errors became minuscule, while the whole process is mostly automated.
Lessons Learned
It’s all about effective communication and testing
Working with Valnes gave us a lot of insights on how to maximise the value of development and what more effective means of communication we should implement as a team. One of the main lessons we learned is the need to document everything when working across different teams. Initially, a lot of information was given to us verbally through various discussions which left a lot of questions on the table in later developments. So in the following projects, we have always put extra effort into documenting our client’s requirements and how we can structure the information in a way that is understandable for both the client and our team.
Secondly, we were reassured about the importance of pre-testing – especially if it involves low-power devices. In such cases, we must measure precisely the necessary voltage and give a detailed valuation of the expected life span regarding the size of the battery.
In this project, we also had to develop a lot of different variants of the product. We were successful in the end, but it came with lots of unexpected integration problems and stress for our development team. Moving on, we have been more mindful about agreeing to build a wide variety of different products and prefer to design a single product, doing that exceptionally well.
Lastly, we now have a wide array of experience in choosing an EMS provider. The experience from building the smart lock gave us a good insight into what is necessary to provide the quality for our client that we set out to achieve. After working with Valnes, we are now well connected with high-quality EMS providers who we are working with to this day.
Our Joint Future
Developing Next-Generation Solutions with Valnes
Today, we are continuing our cooperation with Valnes and still supply our designed devices for them. By now, we have also started to discuss developing the next generation of smart locks and other access systems.
Smart access systems have a lot of room for improvement, and we’re excited to see how we can further advance Valnes’ lock security in our next projects.