Estonia, the most digital country in the world, also has a long history of developing and shaping space science as we know it today. Although the Estonian space program focuses on cyber security and machine learning, Estonian companies are also tapping into the potential of sending technology to space.
One of the recent success stories is a stereo camera that will be part of the NASA Artemis program. Estonian company CrystalSpace was selected to build two cameras that will act as a stereo pair to monitor the operations of a robotic arm that will collect regolith samples from the moon. CrystalSpace partnered with the Tartu Observatory of the University of Tartu, and Krakul, an Estonian autonomous systems development company.
The cameras are part of a robotic arm developed by Maxar Technologies, an earth intelligence and space infrastructure company. The Sample Acquisition, Morphology Filtering, and Probing of Lunar Regolith (SAMPLR) is the first United States-provided robotic arm operated on the surface of Earth’s Moon since the Surveyor missions more than 50 years ago. SAMPLR is one of 12 externally-developed payloads that NASA selected in 2019 as part of the Commercial Lunar Payload Services (CLPS) project, which allows rapid acquisition of lunar delivery services for payloads like SAMPLR that advance capabilities for science, exploration, or commercial development of the Moon.
Although CrystalSpace is a small company from Estonia, they operate in a very specific field, developing and producing nanosatellite parts. The company has developed payloads for satellites like ESTCube-1, Aalto-1, and ESEO. The company was created in 2013 as a spin-off from the student CubeSat project ESTCube-1.
“We already had a proven space technology background right from the start. In addition to developing and selling camera systems, CrystalSpace has participated in various projects, for example, we were part of the ESA BIC Estonia business incubator in 2017, which also added credibility. We built our contact network over time and have also attended various conferences and space events to put ourselves in the picture,” said Pätris Halapuu, CEO of CrystalSpace.
“In the field of space technology hardware, you have to be around for a longer time and show quality, ability, and consistency to be a recognized and trusted player. ESA, NASA, and other space organizations have their own databases of trusted suppliers, and we managed to get into NASA’s supplier database around 2016,” Halapuu added.
Maxar contacted the Estonian company, as they took an interest in the camera models they found in the company’s portfolio that seemed to be a close fit for their purpose. “We then started detailed discussions with them, which lasted almost one year before signing the contract. We were able to discuss everything necessary in time, building a business relationship that reached the result,” added Halapuu.
CrystalSpace developed the camera solution together with Tartu Observatory of the University of Tartu and IoT and autonomous systems development company Krakul. “We had a tight schedule, but since we had worked with our partners on various projects before, we knew we could count on everyone being able to meet the deadlines,” commented Kristjan Tozen, CEO of Krakul. CrystalSpace delivered system integration and the design and optics of the camera in cooperation with Tartu Observatory.
As CrystalSpace already had a working camera model in their portfolio, the key aspect of product development was determining what needed to be adjusted to meet Maxar’s specific requirements. Product development included industrial design, firmware development, electronics development, software development, mechanical design, testing, and verification. Tozen noted that they were fortunate to have excellent partners in Estonia, with several of them also having previous experience with space technology. Krakul handled industrial design, firmware, and electronics development and partnered with Insero for mechanical design and Tauria for software development.
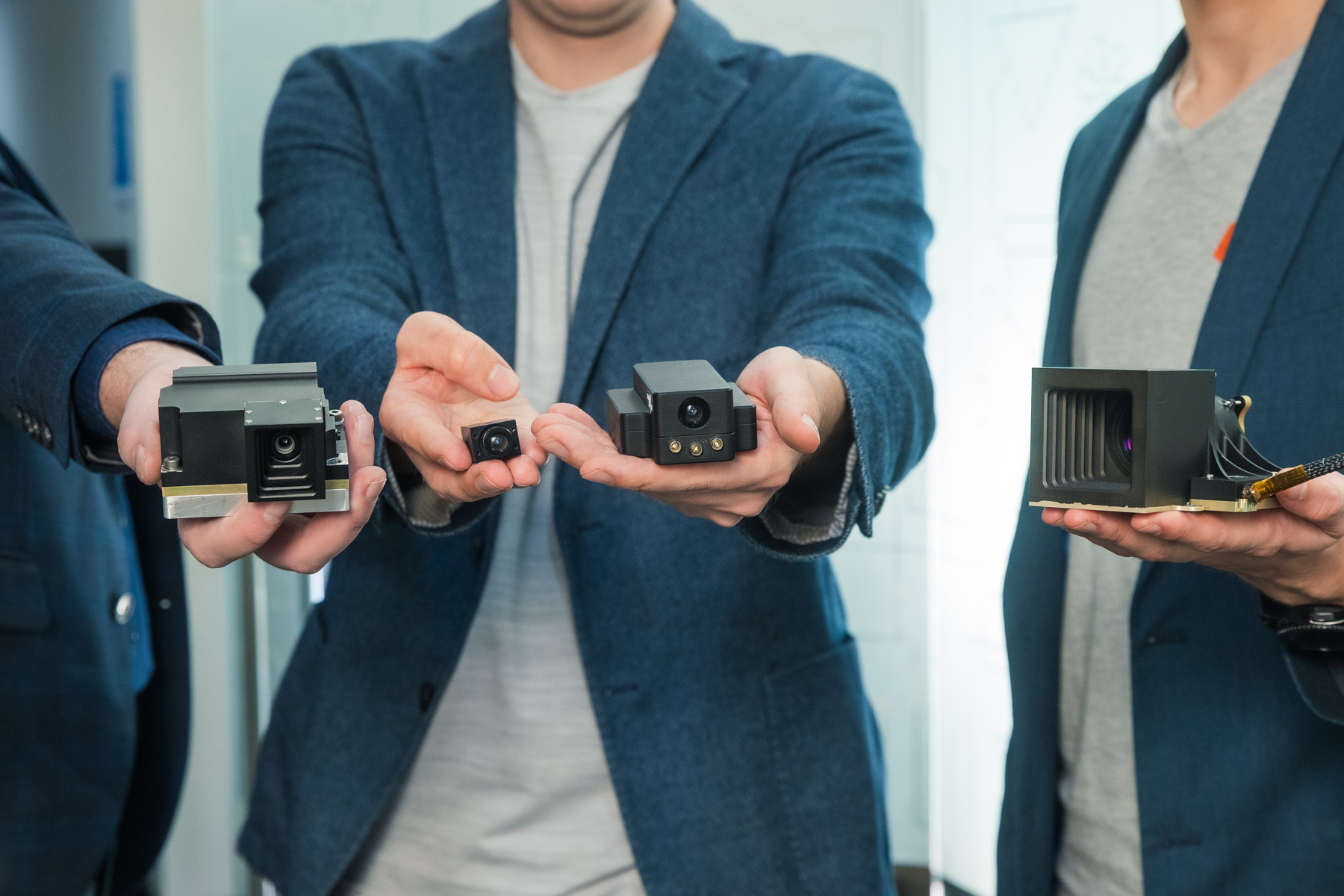
The first step was understanding the constraints and challenges of designing a product for space conditions as well as limitations on the design of the camera body. One of the key takeaways was that the two stereo cameras built for the lunar mission must withstand extreme conditions. “During take-off and the entire mission, the cameras will be subjected to extreme conditions and temperatures from -173 to +100 degrees Celsius on the Moon. Considering the demanding environmental conditions, the engineers had to find suitable surface treatments for the various components to ensure the performance of the electronics and the protection of the camera body itself from environmental influences. The design engineers printed out the exact camera body model with a 3D printer to ensure the electronics, optics, and parts fit together and work reliably. The cameras are made of high-quality aluminum, also used in the aircraft industry,” explained Tozen. During the design process, possible effects of vibration and temperature changes were tested on the design solution with corresponding simulations.
The design engineers had to find suitable surface treatments for the various components to ensure the performance of the electronics and the protection of the housing itself. After introducing the necessary changes, 3D models were printed out to make sure that the electronics, optics, and other parts fit together and worked reliably.
Testing was a crucial part of the process. Before manufacturing the actual cameras, several prototypes were produced and tested. “The production of camera prototypes went according to plan despite the tight schedule. The engineering models successfully passed the first tests at Tartu Observatory of the University of Tartu,” said Tozen. “When sending a product into space, there is no room for malfunction, so ensuring the quality of the product for the time of the mission is of key importance. The developers tested the cameras thoroughly in all stages of the development process and finally in the Tartu observatory,” said Tozen.
The cameras were tested in a thermal vacuum chamber, on a vibration stand, and tested for mechanical shock resistance. The most challenging was to ensure a complete solution, i.e., simultaneous operation of two cameras with all functions.
For the manufacturing of the cameras, Krakul partnered with Incap Electronics Estonia to produce the electronics and Radius Machining to produce the mechanics. Radius produced special aluminum alloy mechanical components for cameras, which were produced using CNC cutting machines. As every gram counts when sending a product into space, the parts were designed to be quite light and thin, and a lot of effort was put into achieving the necessary tolerances.
The two stereo cameras sent to space create a 3D image of the surroundings. “In other words, stereo cameras use two images, making them into a spatial image similar to human vision. In order to effectively use stereo cameras, the cameras needed to be calibrated and characterized very precisely because otherwise, significant distortions occur in the spatial image. To avoid distortions, cameras are developed so that their layout and parameters change as little as possible,” said Halapuu.
After CrystalSpace and Krakul sent the cameras to Maxar Technologies, they started testing the integration of the stereo cameras with the robotic arm that will start taking regolith samples on the Moon to make sure that all systems work flawlessly with each other.
Tozen added: “It is a dream come true for our company to be part of this project. Krakul’s solutions can be found on Earth, in space and the depths of the seas, and now soon also on the surface of the Moon.”
This article was first published in Aktuelle Technik: https://www.aktuelle-technik.ch/in-den-weltraum-iot-in-der-praxis-a-e10ef8e7819de2241026ba194a8b3e4e/
Contact:
press@krakul.eu